Scroll to:
Polyethylene Resistance to Oil and Associated Water
https://doi.org/10.23947/2687-1653-2023-23-1-55-65
Abstract
Introduction. Polyethylene is the most widely used material in various fields of the national economy, and products made of it have essential advantages, such as lightness, insolubility in organic solutions with quite satisfactory strength. However, the mechanism of its destruction is quite complex and depends on the working conditions and substances, which are in contact with it. The research purpose was to study the polyethylene resistance to oil and associated water under the static and dynamic conditions and at room temperature.
Methods and Materials. The research was carried out on a laboratory device for passing various liquids (oil, associated and distilled water) in polyethylene pipes, assembled by the author of the article. While working, methods of statistical and dynamic data processing were applied.
Results. Based on the results of previous experiments, graphs were plotted for the change in the weight and volume of immersed granules over time. They have shown that polyethylene has a quadratic dependence, and diffusion for the three liquids studied in this work (distilled water, accompanying water and oil) is described by Fick's law. This indicates the fact that the rate of liquid diffusion through polyethylene is the key factor.
Discussion and Conclusions. The obtained results have shown that the rate of liquid diffusion through polyethylene is the key factor. Immersion in oil has a greater impact than immersion in associated or distilled water due to the presence of salts. It has been found out that the relative change in the weight and thickness of the polyethylene pipe walls through which oil passes is greater than those through which the associated water passes. Moreover, the microscopic cross sections images in the samples before and after the tests have confirmed the obtained results.
For citations:
Antipas I.R. Polyethylene Resistance to Oil and Associated Water. Advanced Engineering Research (Rostov-on-Don). 2023;23(1):55-65. https://doi.org/10.23947/2687-1653-2023-23-1-55-65
Introduction. Polyethylene is one of the main elements of the olefin family, which is usually characterized by a waxy appearance, chemical inertia and physical properties deterioration at high temperatures. Since polyethylene is a partially crystallized material and does not go into secondary chemical reactions with any liquids, it has no solvents, and its water absorption at ambient temperature is relatively low.
Polyethylene does not dissolve in organic solutions, but it expands at a temperature of more than 70 °C and dissolves in granular aromatic hydrocarbons, it is not affected by oil, fats, kerosene and other hydrocarbons. It is also resistant to aqueous solutions of acids, salts and alkalis [1–5].
Polyethylene is oxidized by nitric acid, which causes a deterioration in the characteristics of the products obtained from it. Oxidation occurs in the presence of ultraviolet rays at ambient temperature, causing final brittleness and deterioration of the mechanical and thermal insulation properties [6–8]. The scientific interest is focused at the practical interaction study of polyethylene and oil, which is a mixture of hydrocarbon materials consisting mainly of compounds containing carbon and hydrogen as well as some elements mixed with hydrocarbons, such as sulfur, nitrogen and oxygen, in addition to metal elements in simple proportions, such as iron, nickel, arsenic and vanadium. Along with them, chlorides salts of land-based minerals as well as their sulfates are present in oil. Moreover, oil contains water in certain percentages, depending on its type and production conditions, and this percentage can increase up to 30 % relative to the total volume of oil, since it is in the form of saturated solutions of sodium chloride, magnesium sulfate and calcium. Carbon dioxide and hydrogen sulfide gases dissolving in water increase its volume. Acid and oxygen, reacting with iron and manganese dissolved in the associated water, form insoluble products. The associated water contains a small percentage of organic chloride salts, not exceeding 50 parts per million [9, 10].
The impurities contained in crude oil (solid materials – salts – water – chemical additives) cause serious risks to the oil refining equipment, its operating time and efficiency. Polymer materials are known to be destroyed in a completely different way than metal materials; therefore, when producing various products from them, it is necessary to take into account their physico-chemical properties and electrochemical reactions.
Plastics cannot dissolve like metals, but they are damaged or destroyed due to swelling, that is, the so-called embrittlement occurs, in which they soften, harden and change colour, which leads to their mechanical properties deterioration.
There are several mechanisms of polymer materials destruction:
- structure swelling;
- dissolution;
- bonds are destroyed under heat, chemical reactions or free radical reactions. The surface layer embrittlement can occur by any one mechanism or by a combination of mechanisms [11–13].
Dissolution and swelling without breaking chemical bonds are the main causes of embrittlement upon contact with impurities, and this process is complex, since small amounts of polymer solution penetrate inside [14], forming a seeping layer with altered physical properties (Fig. 1).
Fig. 1. Layer-structure of embrittlement process
The research objective is to study the polyethylene resistance to oil and associated water at room temperature, both at rest and in motion.
Materials and research methods. Table 1 shows the substances dissolved in oil after its extraction.
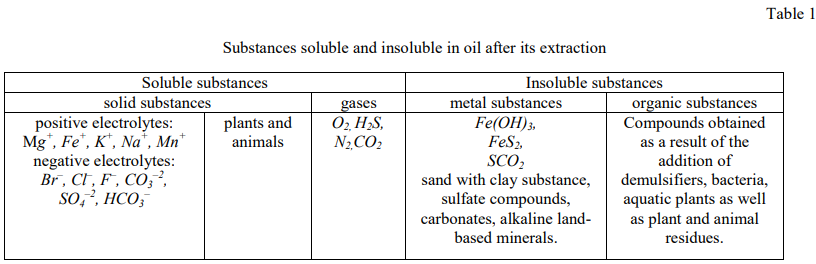
Table 2 shows the composition of the associated water used in the experiments.
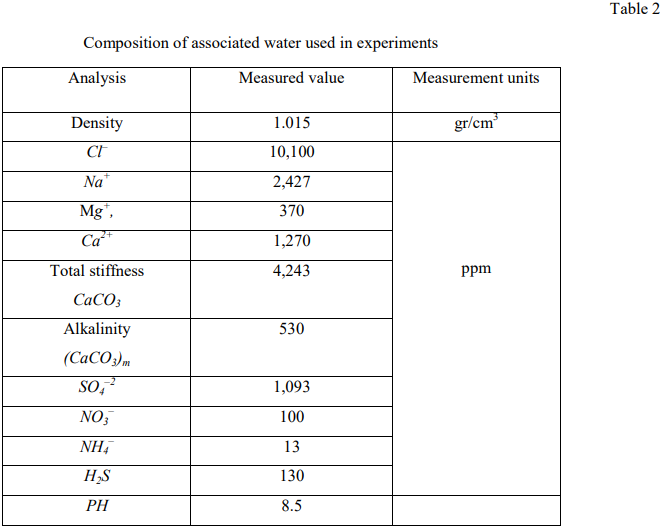
Petroleum alcohol was used as a cleaning agent. The experiments were carried out using granules and pipes made of high-pressure polyethylene HDPE of low density (Table 3).
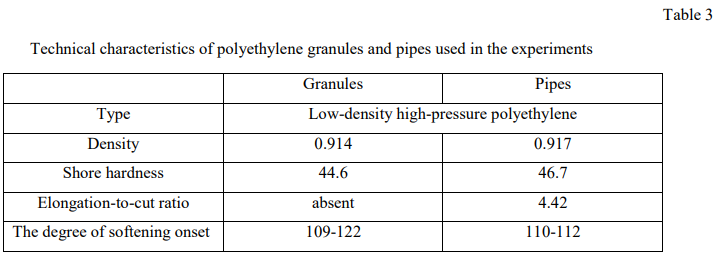
Laboratory instruments. Oil and associated water passed through polyethylene pipes in a laboratory device assembled by the author (Fig. 2). The complex of equipment included:
- sealed glass containers;
- scale with a sensitivity of ± 0.1 g, %;
- electronic micrometer with an accuracy of 1 micrometer; electronic microscope connected to a computer
- An electron microscope connected to a computer.
Fig. 2. Laboratory device for passing oil and associated water in polyethylene pipes
Experiments. In calm mode (immersion method), the sequence of actions when setting up the experiment was as follows:
- weight W1 and volume V1 were determined for several polyethylene granules samples, the characteristics of which are given in Table 3;
- the samples were completely immersed in oil, associated and distilled water in the sealed containers for certain periods of time;
- the taken samples were cleaned;
- the sample weight was determined as W2 and its volume as V2 during the experiment;
- the weight change was calculated as ∆W=W2 – W1 and the volume change – as ∆V = V2 –V1,
- the relative weight change as
and the relative volume change as
were calculated after each sample testing.
In dynamic mode:
- oil and associated water flowed in the polyethylene pipes at a constant speed at the ambient temperature, their weight as W1 and the wall thickness were determined for specific periods of time;
- the pipes were cleaned after each experiment;
- their weight as W2 was determined after the experiment W2, and the wall thickness – after the experiment as X2;
- the weight change was determined as ∆W = W2 – W1, the volume change was as ∆V = V2 – V1, the relative weight change was as
and thickness change was as ∆X after the experiment.
Results and discussion
The weight and volume changes test results of particles immersed in oil, associated and distilled water were summarized in Tables (4–9). A graphical dependence was found for the relative weight and size changes of oil granules immersed in water, associated and distilled water (Fig. 3 and 4).
Fig. 3. Relative weight change of the immersed granules by time
Fig. 4. Relative volume change of immersed granules by time
Figures 3 and 4 show that the time dependence of the relative weight and size changes of polyethylene granules has the character of a quadratic dependence and follows Fick's law in diffusion in the cases of three studied liquids (distilled water, associated water and oil), which indicates that the diffusion speed of liquid through polyethylene is the most important factor.
The relative weight change of granules immersed in the distilled water is not mentioned, but it is rarely noticeable in the associated water and increases more in the oil, as shown in Figure 4. This is due to the fact that salt diffusion significantly effects on the relative weight and volume between the granules immersed in the distilled water, on the one hand, and the granules immersed in the oil and related water, on the other hand.
The test results of the pipe weight and thickness changes, in which oil and associated water flow, are systematized in
Tables 10 and 11. A graphical dependence of the pipe relative weight and thickness changes, through which the oil passes with the associated water flow shown in Figure 5 and 6, was obtained.
The sample cross section micrographs were taken before and after the tests with a 510-time increase and shown in Figure (7).
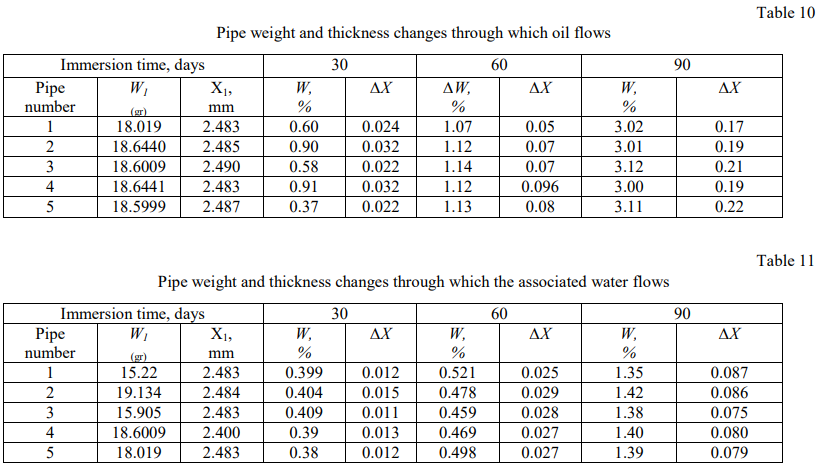
Fig. 5. Pipe relative weight change through which oil and associated water flow, over time
Fig. 6. Pipe relative thickness change in which oil and associated water flow, depending on time period
Due to Figures (6) and Table (12), it is noted that the relative change in the weight and thickness of the polyethylene pipe walls through which oil passes is greater than those through which the associated water passes, which indicates that polyethylene is more affected by oil.
Fig. 7. Sample cross section micrographs before and after tests with a 510-time increase: a — cross section of a clean granule; b — cross section of an oil granule; c — cross section of a pipe with associated water in oil; d — cross section of a pipe immersed in oil; e — inner surface of the pipe with associated water; g — cross section of the pipe immersed in oil after 200 hours; h — inner surface of the pipe immersed in oil
Figure 7 shows cuts of pipe and granules samples before and after the tests, reflecting the surface colour and smoothness of the cross sections subjected to the tests, compared to the clean cross sections, which confirms the previous results obtained due to the basis of the graphs.
Conclusions
The experiments and the results obtained have shown that the liquid diffusion speed through polyethylene is the most significant factor. Immersion in oil has a greater impact than immersion in associated water and distilled water according to the presence of salts.
It has been found out that the relative change in the weight and thickness of the polyethylene pipe walls through which oil passes is greater than those through which the associated water passes, and the microscopic cross sections images in the samples before and after the tests have confirmed the obtained results.
References
1. Antypas I. The Influence of Polyethylene Processing on the Plastic Containers Blowing. Journal of Physics: Conference Series. 2020;1515:042042. 10.1088/1742-6596/1515/4/042042
2. Zakharyan EM, Petrukhina NN, Dzhabarov EG, et al. Pathways of Chemical Recycling of Polyvinyl Chloride. Part 2. Russian Journal of Applied Chemistry. 2020;93:1445-1490. 10.1134/S1070427220100018
3. Chinedu Nwapa, Okunwaye OJ, Okonkwo CL, et al. Mechanical Properties of High Density Polyethylene and Linear Low Density Polyethylene Blend. SSRG International Journal of Polymer and Textile Engineering (SSRG-IJPTE). 2020;7:22-28. 10.14445/23942592/IJPTE-V7I1P103
4. Antypas IR. Improvement of Mechanical Behavior of Neoprene Rubber by means of Glass Fiber. Journal of Physics: Conference Series. 2021;1889:042007. http://dx.doi.org/10.1088/1742-6596/1889/4/042007
5. Wei-Li Wu, Yi-Wen Wang. High Density Polyethylene Film Toughened with Polypropylene and Linear Low Density Polyethylene. Materials Letters. 2019;257:126689. http://doi.org/10.1016/j.matlet.2019.126689
6. Chaudhary AK, Vijayakumar RP. Effect of Chemical Treatment on Biological Degradation of High-Density Polyethylene (HDPE). Environment, Development and Sustainability. 2020;22:1093-1104. https://doi.org/10.1007/s10668-018-0236-6
7. Lethola M, Miettinen IT, Lampola T, et al. Pipeline Materials Modify the Effectiveness of Disinfectants in Drinking Water Distribution Systems. Water Research. 2005;39:1962–1971. http://dx.doi.org/10.1016/j.watres.2005.03.009
8. Antypas IR, Savostina TP. Study of Mechanical Properties of Recycled Polyethylene of High and Low Density. Materiale Plastice. 2021;58:210-215. https://doi.org/10.37358/MP.21.4.5546
9. Zabolotnyi O, Zabolotnyi V, Koshevoy N. Oil Products Moisture Measurement Using Adaptive Capacitive Instrument Measuring Transducers. In book: Nechyporuk M, Pavlikov V, Kritskiy D. (eds.) Integrated Computer Technologies in Mechanical Engineering. 2021;188:81-91. http://dx.doi.org/10.1007/978-3-030-66717-7_7
10. Beglyarovas ÉS, Sokolova A, Bakshtanin M. Change of Indicators of Pollution of Surface Drain of Urban Territories when Carrying Out Construction Work on the Example of the Private Reservoirs of Rivers Likhoborka and Zhabenka. Power Technology and Engineering. 2021;55:1-5. http://dx.doi.org/10.1007/s10749-021-01316-0
11. Martins LS, Mulinari D, Zanini NC. Envelopes with Microplastics Generated from Recycled Plastic Bags for Crude Oil Sorption. Polymer Engineering and Science. 2021;61:2055-2065. http://dx.doi.org/10.1002/pen.25734
12. Ketan Patel, Samir H Chikali, Swaminathan Sivaram. Ultrahigh Molecular Weight Polyethylene: Catalysis, Structure, Properties, Processing and Applications. Progress in Polymer Science. 2021;109:101290. https://doi.org/10.1016/j.progpolymsci.2020.101290
13. Lethola M, Miettinen LT, Lampola T, et al. Pipeline Materials Modify the Effectiveness of Disinfectants in Drinking Water Distribution Systems. Water Research. 2005;39:1962–1971. http://dx.doi.org/10.1016/j.watres.2005.03.009
14. Reye JT, Moore EJ, Riga AT. Dissolution and Swelling Characterization of Diverse Amorphous Polymers by Thermal Mechanical Analysis. In: Proc. Annual Conference of the North American Thermal Analysis Society (NATAS), 2005. P. 1–22. https://www.researchgate.net/publication/343759376_Dissolution_and_Swelling_-Characterization_of_Diverse_Amorphous_Polymers_by_Thermal_Mechanical_Analysis
About the Author
I. R. AntipasRussian Federation
Imad Rizakalla Antipas, associate professor of the Fundamentals of Machinery Design Department, Cand.Sci. (Eng.), associate professor
1, Gagarin sq., Rostov-on-Don, 344003
Review
For citations:
Antipas I.R. Polyethylene Resistance to Oil and Associated Water. Advanced Engineering Research (Rostov-on-Don). 2023;23(1):55-65. https://doi.org/10.23947/2687-1653-2023-23-1-55-65